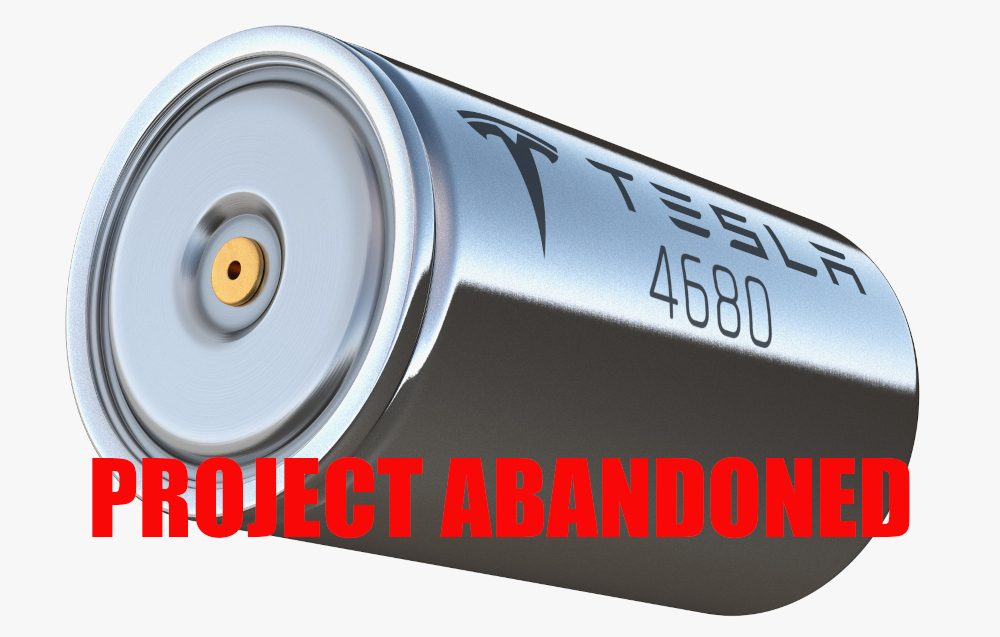
Elon Musk is planning to drop Tesla’s 4680 battery cell initiative by the end of this year due to persistent challenges with energy density, charging performance, and cost control.
Short Summary:
- Tesla struggles to perfect its 4680 battery cell technology since its ambitious launch in 2020.
- Problems with energy density, charging performance, and cost are contributing to the project’s potential abandonment.
- Tesla is looking towards external suppliers, particularly from China, to meet its battery needs.
In the wake of mounting technical difficulties, Elon Musk appears poised to shelve Tesla’s ambitious 4680 battery cell project by the end of the year. This development comes as Tesla continues to wrestle with the challenge of perfecting a battery that was expected to be a game-changer in the electric vehicle industry. Launched with considerable fanfare during Tesla’s Battery Day in September 2020, the 4680 battery’s promise of a fivefold increase in energy density, a 16% increase in range, and a 14% reduction in cost captivated developers and enthusiasts alike.
However, the groundbreaking cylindrical battery, measuring 46 millimeters in diameter and 80 millimeters in height, has been fraught with technical obstacles, leading to delays and escalating costs. In February, Musk already pivoted away from a $25,000 electric car target, choosing instead to focus on the development of autonomous robotaxis. The latest challenge to Tesla’s 4680 project involves a technical quandary that could cause the batteries to collapse during use, as revealed by sources close to the matter.
Reports from June 26 highlighted that Tesla is contemplating ceasing the production of 4680 batteries at its GigaTexas factory due to subpar energy density and charging performance, alongside higher-than-anticipated costs. Should cost reductions not align with projections by the year’s end, Tesla is set to procure batteries from external suppliers.
This shift in strategy is not entirely unexpected. Initial enthusiasm for the 4680’s innovative design gave way to the reality of manufacturing complexity and cost issues. Tesla’s attempt to dry coat anodes and cathodes—a process intended to streamline and reduce energy costs—has proven a substantial bottleneck in mass production. Despite Musk’s assertion in a 2021 IEEE Spectrum interview that the company was near resolving these manufacturing kinks, significant hurdles remain.
Technical Hurdles and Cost Overruns
One cannot overlook the considerable effort and resources already invested in the 4680 battery cells. The goal was clear: establish a vertically integrated, in-house battery production line that could drive down costs and boost vehicle range. Yet, despite producing over 50 million units by June 2023 at the Texas Gigafactory, the 4680 batteries have not met cost targets nor performance benchmarks when compared to competitor cells from the likes of LG and Panasonic.
“We are continuously facing technical challenges with the 4680 battery cells, particularly in aspects of energy density and manufacturing cost,” said Lars Moravy, Tesla’s Vice President of Vehicle Engineering, during the Q1 financial results announcement.
Research from China International Capital Corporation (CICC) indicated a slow but steady yield improvement in 4680 battery production. Nevertheless, the ambitious cost reduction goals remain elusive. Rivals like CATL and BYD have lowered their production costs to RMB 0.4/Wh, while estimates suggest Tesla’s 4680 costs hover between RMB 0.8-1/Wh, still significantly higher than competitors.
Exploring External Partnerships
In light of these challenges, Tesla has increasingly turned to external suppliers to mitigate costs and address supply chain issues. Specific attention has been given to Chinese companies. Since the second half of 2023, Tesla has begun sourcing positive electrode rolls from second-tier Chinese firms and transported them to the Texas factory for final battery assembly. These strategic partnerships are projected to continue accelerating Tesla’s battery production throughout 2024.
“Tesla is getting more pragmatic about the external sourcing of battery components. It’s an essential step to ensure we meet growing demands while battling cost and supply chain issues,” a Tesla insider stated.
Musk acknowledged these difficulties at Tesla’s 2024 shareholder meeting, admitting that the cost and production efficiency targets for the 4680 cell remain arduous. However, he expressed confidence in Tesla’s continuous progress in battery technology, even hinting at a broader strategic pivot to integrate more external suppliers to sustain production volumes and meet the burgeoning EV market demand.
Future Prospects and Strategic Realignment
With the automotive industry ever-evolving, Tesla’s competitive edge in battery technology is crucial. While the 4680 project sits at a critical junction, continuous innovations in manufacturing processes and strategic partnerships could still steer Tesla towards overcoming these challenges. Tesla’s potential cooperation with companies such as Ningbo Ronbay New Energy Technology Co., Ltd., and Suzhou Dongshan Precision Manufacturing Co., Ltd., underscores a pragmatic approach to achieving cost reductions and performance improvements.
The larger picture also involves significant investments in new production lines and expansion projects. The Nevada Gigafactory’s ongoing expansion includes facilities dedicated to the 4680 battery cell format, aiming for a capacity of 100 GWh per year, which would supply batteries not only for Tesla’s vehicles but also for the anticipated production of the Tesla Semi truck.
In the constantly shifting sands of the automotive and energy industries, Tesla remains a formidable player, continuously pushing the boundaries of what is possible. Whether or not the 4680 battery cell becomes the linchpin of Tesla’s EV dominance, the relentless drive for innovation and efficiency stays at the core of Elon Musk’s strategy. The coming months will be critical as Tesla navigates the technical, logistical, and market challenges, striving to maintain its leadership in the electric vehicle revolution.
Under the surface, these developments reveal the intricate challenges and potential of the EV industry’s future. Tesla’s ability to adapt, whether by revisiting technical designs or leveraging global partnerships, will indelibly shape the trajectory of its ambitious 20 million car production target by 2030.
However, the narrative is not solely about Tesla’s technological advancements. Musk’s vision encompasses a broader economic and geopolitical context. As countries push for cleaner energy alternatives, batteries remain the fulcrum of this transformative shift. If Tesla can align its internal production capacities with external supplier efficiencies, it could redefine not just its business model but the entire supply chain dynamics of the EV industry.
Conclusively, while the 4680 battery cell project faces a rocky path ahead, its journey encapsulates the ethos of modern industrial challenges—innovation matched with pragmatism, ambition tempered by reality. The automotive world watches closely as Tesla steers through these uncharted waters, with the 4680 battery symbolizing the high stakes and equally high hopes of the electric future.
Sources:
https://www.theinformation.com/articles/teslas-future-was-all-about-the-battery-until-it-wasnt
https://www.energytrend.com/news/20240628-47693.html
https://spectrum.ieee.org/tesla-4680-battery
https://cleantechnica.com/2024/06/24/elon-musk-teslas-4680-batteries-at-cost-parity-with-cheapest-suppliers-by-end-of-year/
https://www.electrive.com/2024/01/25/teslas-4680-cells-production-is-no-longer-a-bottleneck/
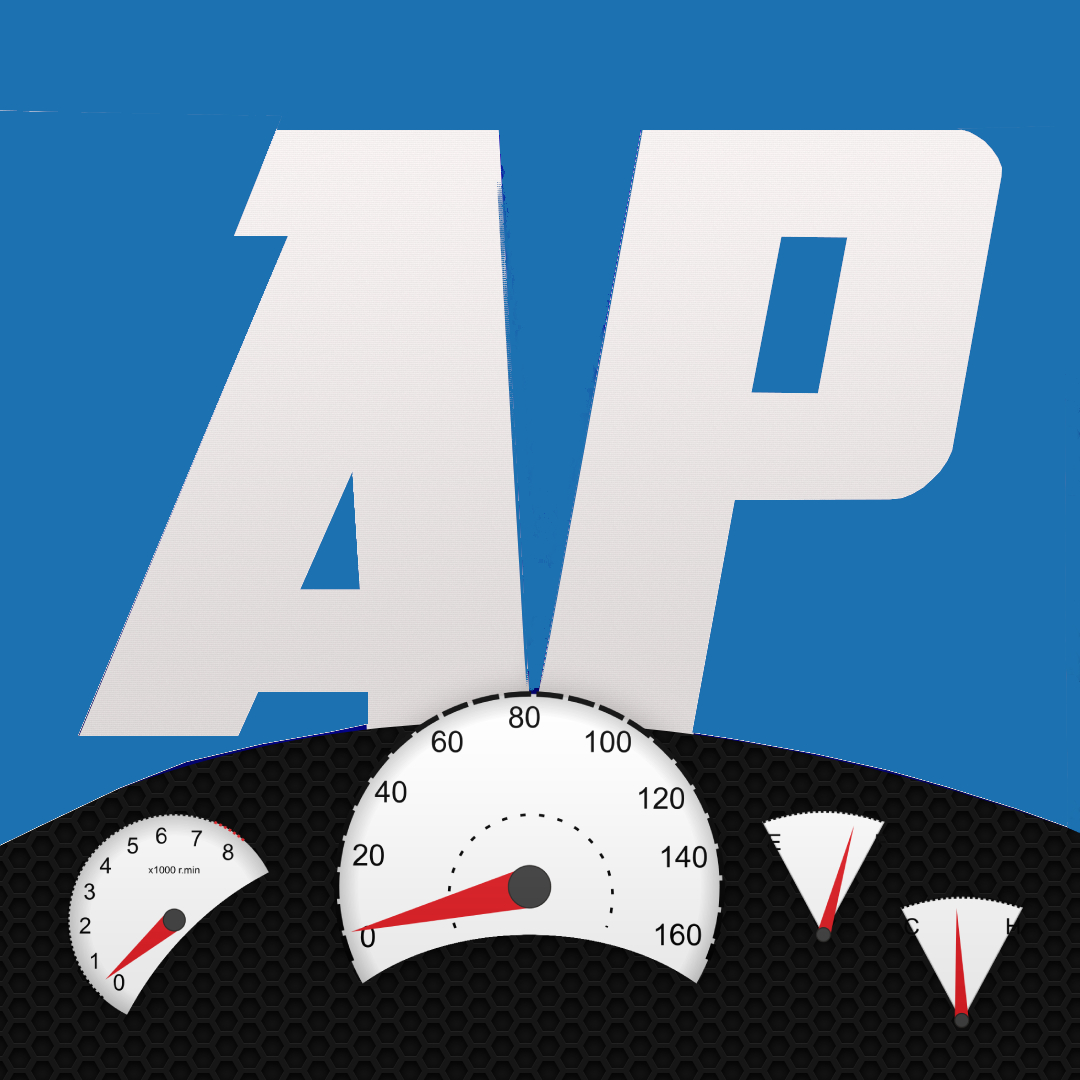
The AutoPros.online team is dedicated to bringing you high quality automotive content for professionals and car enthusiasts, with topics like auto detailing, performance modifiations, repairs and automotive news.